How I Made It: Doug Schulte, Select Machining Technologies
Doug Schulte was introduced to machining as a young child, often visiting his father at the LeBlond Machine Tool company where he worked in Cincinnati. Here, Schulte — who ended up dedicating his entire career to the industry — shares some of the key insights he’s discovered along the way.
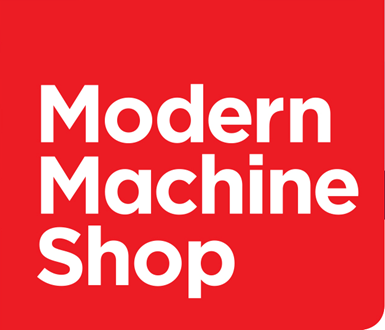
To some of his friends, Doug Schulte is known as “machine tool Google.” His encyclopedic knowledge of the specs and mechanics of machine tools comes from a lifetime spent in the industry. It all started with his dad, John, who joined machine tool manufacturer LeBlond in the early 1950s.
I GUESS YOU COULD SAY I was born into this business. My dad started working for LeBlond around 1953, and after 32 years he went to work for a small company who was the LeBlond Makino distributor at the time, the R.O. Deaderick Company [now part of The Morris Group].
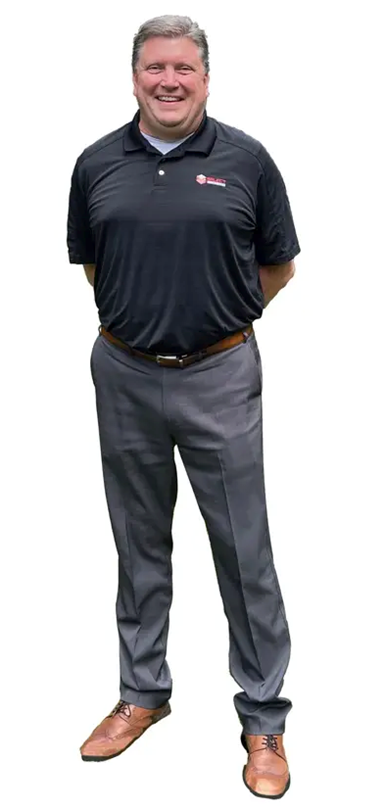
Doug Schulte, Senior Product Manager for Select Machining Technologies. Photo Credit: Modern Machine Shop
I REMEMBER GOING TO THE FACTORY with him where they had several different lathes on the floor. If I had a science project at school where I needed to make something, we would go to LeBlond and make it. The idea that you could cut metal was astounding to me.
I QUICKLY REALIZED that I’m not the manufacturing engineering type of guy. So I went to Cincinnati Technical College (now Cincinnati State), which had a program called Industrial Sales and Marketing.
SINCE ‘88 I’VE BEEN WITH THE MORRIS GROUP. But I didn’t differentiate it. It always felt like I was working for Dad. And I continued to work for Dad until he retired in 2001.
IF I SELL SOMEONE SOMETHING AS SIMPLE AS A SAW, and that saw was a good saw, when that person did get around to buying a lathe or a machining center, I was probably going to get the phone call. That was my thinking. I never want to turn a customer over to a competitor and say, “Go buy from them.”
I WAS EMBARRASSED EARLY ON IN MY SALES CAREER with a customer in Tennessee. An engineer asked me a question and my answer was incorrect. He called me on it. After I left, I said to myself that I’m never going to let that happen again. Ever since, if I was promoting a machine to a customer, I would know every aspect of that machine forward and backward. I would know the specs better than the manufacturer.
MY DAD WOULD ALWAYS BE ASTOUNDED because I hate to read. I’ve got books on my bookshelf but there are very few of those books that I’ve read. But I’ll sit down with a machine tool manual and read it cover to cover.
EARLY IN MY CAREER, Dad pointed out that I asked a lot of questions in the sales meetings. But I noticed the older sales guys would never do that. So I asked Dad why no else asked questions. He said, “Well, they don’t want to admit that they don’t know the answer.”
IT’S A FANTASTIC INDUSTRY. If the country’s not manufacturing something, the country’s not surviving. And it’s a fun industry — the kind of things we do, the kind of things we make, the kind of parts you see, the people you deal with. I’ve developed friendships all over the world. There are (machine tool) builders that I don’t represent anymore that still wish me happy birthday every year. You’re tied to a very small industry that has so much impact on everybody’s lives. And most people don’t know it.
Related Content
How to Reduce Cycle Times by 70% and More on Your Existing CNCs and Dramatically Improve Tool Life Too
By employing advanced high efficiency milling techniques for the entire machining routine, SolidCAM’s iMachining technology can drastically reduce cycle times while vastly improving tool life compared to traditional milling.
Read MoreInside an Amish-Owned Family Machine Shop
Modern Machine Shop took an exclusive behind-the-scenes tour of an Amish-owned machine shop, where advanced machining technologies work alongside old-world traditions.
Read MoreGrinding Wheel Safety: Respect The Maximum Speed
One potential source of serious injury in grinding comes from an oversight that is easy to make: operating the wheel in an over-speed condition.
Read MoreUnderstanding Swiss-Type Machining
Once seen as a specialty machine tool, the CNC Swiss-type is increasingly being used in shops that are full of more conventional CNC machines. For the newcomer to Swiss-type machining, here is what the learning curve is like.
Read MoreRead Next
Obscure CNC Features That Can Help (or Hurt) You
You cannot begin to take advantage of an available feature if you do not know it exists. Conversely, you will not know how to avoid CNC features that may be detrimental to your process.
Read MoreThe Cut Scene: The Finer Details of Large-Format Machining
Small details and features can have an outsized impact on large parts, such as Barbco’s collapsible utility drill head.
Read More3 Mistakes That Cause CNC Programs to Fail
Despite enhancements to manufacturing technology, there are still issues today that can cause programs to fail. These failures can cause lost time, scrapped parts, damaged machines and even injured operators.
Read More