When 3D printing contract manufacturer Cumberland Additive recently acquired the metal additive manufacturing operations of Stratasys Direct, the move doubled the company’s number of metal additive manufacturing (AM) machines and gave the company an additional production facility in its home region of Austin, Texas. However, this new facility became not the second, but rather the third location for Cumberland. Prior to the acquisition, Cumberland opened a location far from its Texas headquarters at Neighborhood 91, a Pittsburgh, Pennsylvania, industrial park that is focused on additive manufacturing.
Now, two years after opening the Pittsburgh site, Mark Straszheim, the Cumberland regional director who worked to stand up the facility, has various observations about how best to leverage its AM capabilities across sites in different regions of the country. While shifting work digitally between sites for distributed manufacturing is an option for which 3D printing is well suited, and an option the company has successfully employed with this facility, Straszheim says the “digital transparency” of employees has delivered even greater value. This is particularly notable in the way the machining expert at this site supports jobs across the country.
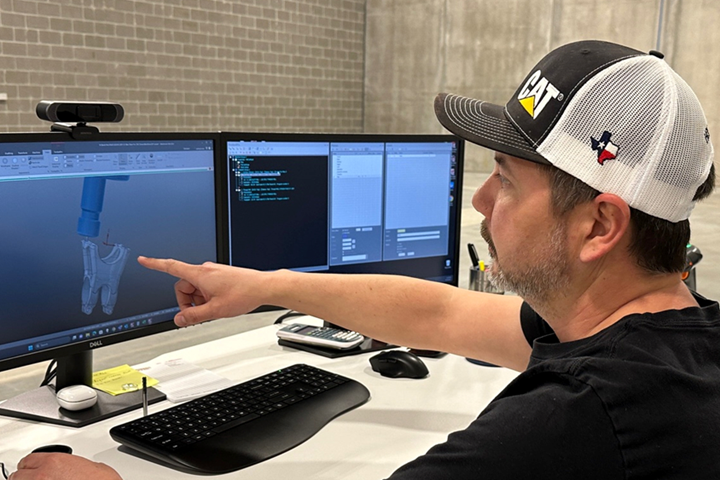
Victor Ross is one of three CNC programmers working for Cumberland Additive, and he is the one who works the farthest from the majority of the company’s CNC machines. Most of the company’s machine tools are in Austin, Texas, while Ross works at a Pittsburgh location where just one five-axis machine is located. Photo: Cumberland Additive.
Opening a Pittsburgh Site and Joining Neighborhood 91
One of the reasons for establishing a location so far from Cumberland’s Pflugerville, Texas, headquarters was the concept for Neighborhood 91 — among the most unusual industrial parks in the country. Becoming a tenant at this Pennsylvania campus would bring direct proximity to other additive manufacturing companies. (Cumberland enjoys this benefit at its headquarters location as well. Its neighbor is AM equipment provider EOS.) Opening a site here would also mean establishing a location geographically closer to customers in the Northeast. The initial questions focused on how to imagine this northern sister site.
According to Straszheim, “We were asking ourselves: Do we make it a focus factory? Or do we have production at one site and R&D at the other?”

Neighborhood 91 is an unusual industrial park, devoted exclusively to additive manufacturing. Cumberland’s location is at the far left of this photo. Other tenants seen here: cold spray AM specialist HAMR Industries, materials supplier Metal Powder Works and locomotive component maker Wabtec. Learn much more in this article about Neighborhood 91.
The answer the company found was to establish a facility that is like Pflugerville in terms of its role — that is, both 3D printing and postprocessing, both production and prototyping — but also distinctly flavored to match to special possibilities of the Pittsburgh location.
For example, of the two powder bed fusion metal AM machines installed at the newer site, one of them, an SLM 500 from what is now Nikon SLM Solutions, closely matches a machine from the same provider that is used by the very first Neighborhood 91 tenant, locomotive component producer Wabtec. The Cumberland machine has the same X-Y travels as Wabtec’s SLM model; it differs just in Z.
Wabtec and Cumberland are not competitors. Therefore, the benefits of two neighbors having very nearly the same additive machine have been apparent for both. Pittsburgh manufacturing engineer Kyle Kubovcik says, “We each have better access to replacement parts, and our two teams together make up a larger pool of experience and expertise on this machine.” Cumberland also has served Wabtec by machining some of its parts when the latter’s machining center was overcommitted.
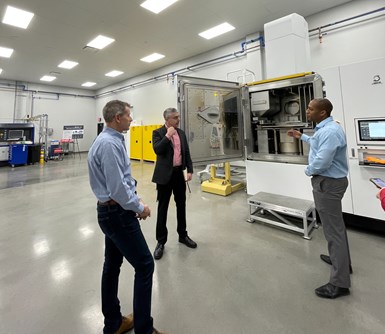
Cumberland Additive has two metal additive machines and processes at its Pittsburgh location. The Nikon SLM Solutions laser powder bed fusion machine (in the background and at the top of this page) closely matches the capabilities of an SLM machine used by a Neighborhood 91 neighbor. The JEOL electron beam melting machine is overseen by JEOL applications engineer Jonathan Buckley, who works at this facility. Buckley is at right, seen here with Cumberland's Mark Straszheim (left) and me.
The other powder bed machine at Cumberland’s Neighborhood 91 location is a JAM-5200 electron beam melting (EBM) system from JEOL, a company relatively new to the U.S. market. Cumberland is a partner supporting the company’s introduction to the U.S., and a JEOL applications engineer, Jonathan Buckley, works here essentially as an adjunct Cumberland team member. This is another valuable use the company has found for the Neighborhood 91 location: With its proximity to the Pittsburgh International Airport (the airport is one of the site’s landlords), it is an ideal locale for hosting a relationship such as this that needs to allow for visitors to the site to see machine demos.
These two machines together are a small share of Cumberland’s AM capacity overall — the company has 35 powder bed fusion systems total. Similarly, a five-axis machining center from Haas Automation at the Neighborhood 91 site is just one of 25 CNC machine tools throughout the organization. Yet the share of personnel and talent in Pittsburgh is much greater. Kubovcik is one of six people doing similar AM engineering work for the company. Much of his time is focused on work performed in Texas. And for Pittsburgh CNC programmer Victor Ross, this is even more true — he is one of three CNC programmers in the company. He writes programs for the Neighborhood 91 machining center and runs this machine, while giving more than half of his time to programming work for Texas CNC machines.
Digital Transparency Empowers Multi-Site Manufacturing
This is what Straszheim means by digital transparency, his version of it at least. It simply should not matter much, if at all, where an engineering or programming employee is located. This employee transparency is a necessary and perhaps underappreciated requirement of a distributed manufacturing model. In additive, part files can be sent digitally for production wherever there is the right type of 3D printer and secure infrastructure. And in AM, the ratio of expert staffing to the number of machines is smaller than practically any production process. Put these two points together, and what they mean is that AM personnel located anywhere (except for the ones physically tending the machines) need to be able to serve production that is also occurring anywhere. And this applies not just to 3D printing, but also to CNC machining.
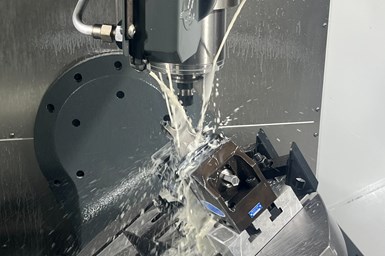
Machining is a vital capability to have on-site, Straszheim says. Because of the digital transparency of Cumberland's organization, the CNC programming expert based in Pittsburgh actually spends the majority of his time writing programs for the company's machine tools in Texas. Photo: Cumberland Additive.
In metal part production, machining is part of AM — and this is why Ross spends so much of his time programming for Texas machine tools.
Doing this is not without challenge, he notes. “The difficulty in programming at a distance comes from just not being able to hold the part in my hand,” he says. “The clamping or approach strategy I am imagining maybe doesn’t work.” Generally, it is not long before a misperception such as this is seen and addressed. Still, it speaks to how a different quality of programmer is needed for this role, possessing a certain extra capacity to spatially imagine an abstract form.
The value of that kind of acuity speaks to a larger shift Straszheim sees. It is pronounced in AM, yet he believes it is apparent in all fields harnessing technology’s freedom to do more with fewer and more dispersed staff. “The challenge of manufacturing today,” he says — and the challenge of small business — “is finding employees able to thrive using a broad range of abilities and talents.”
More From This Author
Peter Zelinski has written for Modern Machine Shop for more than 25 years. Today he reports on the advance of industrial 3D printing as editor-in-chief of Additive Manufacturing Media. Find his work in Additive Manufacturing magazine, in The BuildUp newsletter, and on The Cool Parts Show, which he co-hosts. SUBSCRIBE HERE
Related Content
How to Successfully Adopt Five-Axis Machining
While there are many changes to adopt when moving to five-axis, they all compliment the overall goal of better parts through less operations.
Read MoreHigh RPM Spindles: 5 Advantages for 5-axis CNC Machines
Explore five crucial ways equipping 5-axis CNC machines with Air Turbine Spindles® can achieve the speeds necessary to overcome manufacturing challenges.
Read MoreLean Approach to Automated Machine Tending Delivers Quicker Paths to Success
Almost any shop can automate at least some of its production, even in low-volume, high-mix applications. The key to getting started is finding the simplest solutions that fit your requirements. It helps to work with an automation partner that understands your needs.
Read MoreInverting Turning and Five-Axis Milling at Famar
Automation is only the tip of the iceberg for Famar, which also provides multitasking options for its vertical lathes and horizontal five-axis machine tools.
Read MoreRead Next
3 Mistakes That Cause CNC Programs to Fail
Despite enhancements to manufacturing technology, there are still issues today that can cause programs to fail. These failures can cause lost time, scrapped parts, damaged machines and even injured operators.
Read MoreThe Cut Scene: The Finer Details of Large-Format Machining
Small details and features can have an outsized impact on large parts, such as Barbco’s collapsible utility drill head.
Read More