For Manufacturers, Storage Is an Opportunity for Automation and for Industry 4.0
A maker of automated storage and retrieval systems founded in Europe finds that the leading rationale for adopting these systems is different in the U.S.
This automated storage and retrieval system used in Modula’s own Franklin, Ohio, facility is 52 feet tall and includes 100 trays for storage.
What is the most labor-intensive task manufacturing employees perform? Even in sophisticated manufacturing facilities using a high degree of automation, the answer might be this: look for stuff. That is, seek and obtain the items they need to do their work.
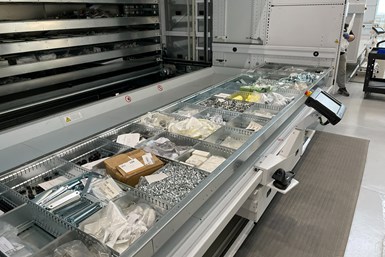
Here is one tray within the 100-tray system. Storing many different types of objects is an important benefit, but controlling and tracking this inventory is equally important.
Storage unintentionally creates drains on time and effort. The best thing to do with bulky resources that are not required immediately for production is to get them out of the way, and the most natural way to do this is to store them on shelves. But then, when the resource is again needed — whether the resource is a tool, raw material, a set of fasteners or other supplies — the one who needs it will have to go to the shelves to get it; search the shelves to find it; and likely enlist the aid of someone with a towmotor in order to retrieve it.
Increased recognition of this drain on capacity is spurring the adoption of automated storage and retrieval systems, says Antonio Pagano, CEO of Modula USA, a provider of vertical storage systems manufactured to order for industrial facilities (tailored, for example, to the extent of a facility’s available ceiling height). Shelves, as companies are coming to see, represent an important opportunity for automation.
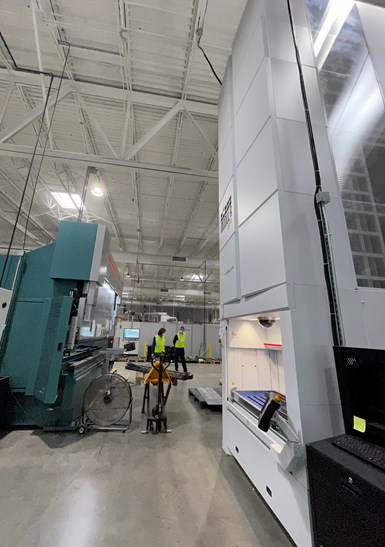
How the storage system is used in Modula's production: An automated storage unit near a press brake stores and organizes press brake tooling.
This is a distinctly North American insight. “In Europe, we had a leg up because of floorspace limitations,” he says. Modula was founded in Italy. Among their earliest adopters, the company’s systems made sense as a solution for using plant space more efficiently. But in North America, floorspace is more available; preserving it is less of a concern. Yet there is a growing premium on employee attention and labor hours. “In the U.S., we started to make inroads once we realized floorspace is not the issue — we have an automation solution instead.”
In fact, an automated storage and retrieval system is a foundation for widespread automation throughout the facility. Each system consists of a vertical set of moving trays (in vertical increments of 200 mm, but variable for objects of different heights), with each shelf delivered as needed to a fixed retrieval area at human level near the base of the system. Delivering every stored object to the same location creates a natural fit with other automation systems. Example: A robot could retrieve an item from the vertical system and place it on an automatic guided vehicle for delivery where it is needed.
But as much as it is a foundation for plant-wide automation, the automated storage and retrieval system is also a foundation for Industry 4.0. As Pagano notes, data from the unit provide both greater control over, and greater insight into, the production process.
Knowing when each tool is retrieved from the system provides an automatic way to track tool use and flag tools for replacement as they near the end of their expected life.
“You can restrict particular employees to particular trays,” he says. “You can also track how many times a given object is retrieved.” An example of this is in use in Modula’s production facility in Franklin, Ohio. An automated storage and retrieval system holds tooling for a nearby press brake. Tracking the retrieval for each press brake die allows the engineering team to know precisely when each tool is nearing the end of its expected life.
This last point might prove to be the ultimate reason why the automated systems are adopted, Pagano says. Floorspace is valuable. Labor is more valuable still. But in an environment of increasingly more tightly controlled production of increasingly valuable products, the knowledge of how a shop’s resources are being deployed might be the most valuable benefit of all.
Related Content
Inside the Premium Machine Shop Making Fasteners
AMPG can’t help but take risks — its management doesn’t know how to run machines. But these risks have enabled it to become a runaway success in its market.
Read MoreBuilding an Automation Solution From the Ground Up
IMTS 2022 provides visitors the opportunity to meet with product experts to design automation solutions from scratch.
Read More4 Steps to a Cobot Culture: How Thyssenkrupp Bilstein Has Answered Staffing Shortages With Economical Automation
Safe, economical automation using collaborative robots can transform a manufacturing facility and overcome staffing shortfalls, but it takes additional investment and a systemized approach to automation in order to realize this change.
Read MoreWhich Approach to Automation Fits Your CNC Machine Tool?
Choosing the right automation to pair with a CNC machine tool cell means weighing various factors, as this fabrication business has learned well.
Read MoreRead Next
Obscure CNC Features That Can Help (or Hurt) You
You cannot begin to take advantage of an available feature if you do not know it exists. Conversely, you will not know how to avoid CNC features that may be detrimental to your process.
Read More3 Mistakes That Cause CNC Programs to Fail
Despite enhancements to manufacturing technology, there are still issues today that can cause programs to fail. These failures can cause lost time, scrapped parts, damaged machines and even injured operators.
Read MoreThe Cut Scene: The Finer Details of Large-Format Machining
Small details and features can have an outsized impact on large parts, such as Barbco’s collapsible utility drill head.
Read More