Kitamura's Five-Axis Machining Center Promotes Accuracy
Kitamura’s Mytrunnion-5G five-axis vertical machining center is designed for maximum accuracy in and capability for complex five-axis machining.
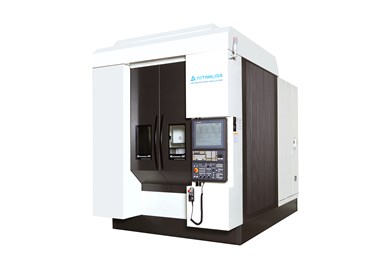
Kitamura Machinery has expanded its Mytrunnion five-axis lineup with the Mytrunnion-5G five-axis vertical machining center. This machining center focuses on speed, rigidity and flexibility in complex 5-axis machining.
The Mytrunnion-5G’s induction-hardened solid box way construction dampens vibrations, while the dynamic double column construction supports the Y-axis throughout its entire movement. A high-precision worm wheel and shaft drive the A-axis fully integrated trunnion table (-120 to +30 degrees), which the company says benefits stiffness and stability. A standard 20-20,000 rpm #40, four-step gear driven, dual-contact spindle delivers strong low-end torque and high-end fine finish capability for enhanced machining flexibility. The 20 HP/AC spindle motor’s maximum cutting torque is 201.4 foot-pounds, and an efficient oil chiller system minimizes thermal displacement and maximizes spindle life. Kitamura’s patented triangular cross rail evenly distributes headstock weight and cutting forces for chatter-free machining, improving accuracy and surface finish.
The Mytrunnion-5G’s work envelope measures 630 mm (24.8”) x 500 mm (19.7”), with a table load capacity of 400 kg (880 lbs) and a sliding ceiling cover to improve access for medium to large parts.
A standard, high-precision package includes positioning accuracies of ±0.001 mm (±0.000039”) with full stroke and repeatability ±0.0005 mm (±0.00002”); a built-in trunnion-style tilting table; ballscrew cooling; Heidenhein linear and rotary scale feedback in the X, Y, Z, fourth and fifth axes; and Kitamura’s IAC System 1 thermal compensation system to control the effects of heat displacement and ensure continuous machining accuracy.
A standard double-decker chip conveyor and filtration system, 220 psi coolant through the spindle and base wash and overhead wash shower coolant provide chip evacuation filtration to 100 microns.
Kitamura’s Arumatik-Mi Control offers 1,680-block lookahead and processing speeds of 2,800 blocks per second for faster machining of more complex workpieces. A customizable, icon-driven touch screen offers a user-friendly, expandable control environment.
Related Content
-
Palmgren Launches Combination Bench Lathe, Mill
The 11" bench engine lathe and gear head mill is able to handle a wide range of turning, milling and drilling operations typically found on much larger machinery.
-
Volumetric Accuracy Is Key to Machining James Webb Telescope
To meet the extreme tolerance of the telescope’s beryllium mirrors, the manufacturer had to rely on stable horizontal machining centers with a high degree of consistency volumetric accuracy.
-
Choosing a Five-Axis Machine Tool With Automation in Mind
While much focus is placed on the machinery that moves parts, the features most important for automating five-axis machining are arguably found in the machine tool itself.