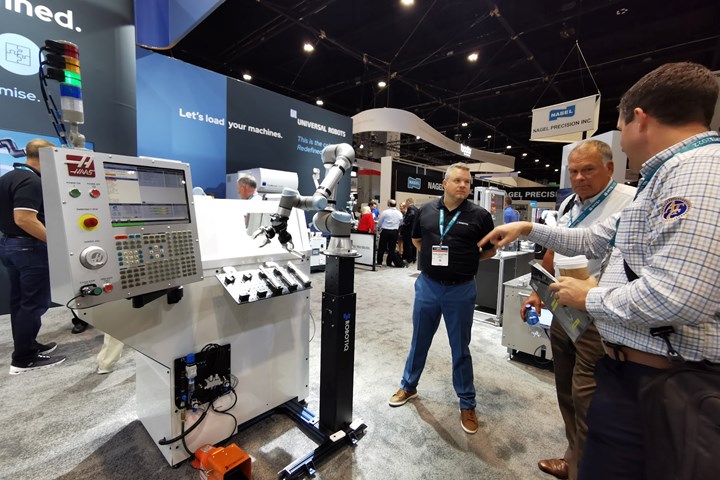
Take his example of Manufacturing Execution Systems. “We are starting to see MES software that not only tracks the progress of jobs but can also handle if/then commands.” This means that these software suites can automate the scheduling of shipments, material orders and even jobs. Once a machine tool finishes a run of parts, the system can alert shipping, print labels, send out a message to the customer, and notify the machinist on the shop floor of the next job. “Automation is not just about moving the parts,” Shinbara says. “It is about smoothing the entire manufacturing process, and now that includes helping with the front office work.”
“If you are wondering whether or not to invest in any technology, then investing into connectivity will make everything else smarter, more effective and more easily updated in future.”
Another job that is seeing more digital tools doing the grunt work is in quoting manufacturing jobs. While the usual process for quoting a job involves one of the most experienced engineers or machinists at the shop taking hours to track down materials on hand, call suppliers and figure out how to fit the job into the schedule, modern software solutions can collect that data and provide it to the quoter without forcing them to do any legwork. “You can’t start a job until the customer accepts your offer,” Shinbara says. “Software is already here that simplifies this process and reduces the time it takes.”
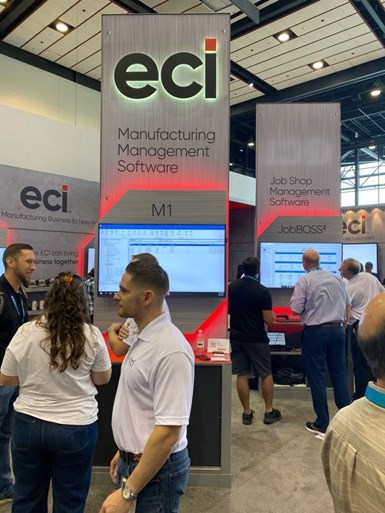
Keeping Your Shop Connected in the Cloud
Machine monitoring is also coming into its own. The data generated by machine tools, smart cutting tools, and nearly every other kind of manufacturing equipment is staggering, and manufacturers are putting it to use. “With some examples, separate monitoring systems are feeding into a single device,” says Shinbara. “This device feeds data to the shop owner, or even analyzes the data itself.” Monitoring systems like this are not only providing raw data, but reporting specific issues and including known solutions in reports. These systems can identify patterns that separates important information from the noise.
And it is not just monitoring systems: Connectivity can benefit shops in numerous ways. It could be as simple as the robot arm sharing a control with the machine tool, making it easier to program an operation. “What is frequently overlooked is how fundamentally important connectivity is, both in terms of communications networks, and in terms of standards, drivers, libraries and operating systems,” says Andra Keay, managing director of Silicon Valley Robotics. “If you are wondering whether or not to invest in any technology, then investing into connectivity will make everything else smarter, more effective and more easily updated in future,” Keay says.
Data storage and security are also key challenges that many manufacturing facilities face. It is especially important when working on government contracts, and it can be expensive to manage your own servers and IT security team. This is why cloud-based technologies are becoming more and more important to manufacturers: by contracting with cloud-based software, a facility offloads the work of maintaining and protecting its data to professionals who are dedicated to that task. “You need to invest in going digital and connecting to the cloud,” says Keay.
Related Content
Shop Moves to Aerospace Machining With Help From ERP
Coastal Machine is an oil and gas shop that pivoted to aerospace manufacturing with the help of an ERP system that made the certification process simple.
Read More5 Stages of a Closed-Loop CNC Machining Cell
Controlling variability in a closed-loop manufacturing process requires inspection data collected before, during and immediately after machining — and a means to act on that data in real time. Here’s one system that accomplishes this.
Read MoreHow this Job Shop Grew Capacity Without Expanding Footprint
This shop relies on digital solutions to grow their manufacturing business. With this approach, W.A. Pfeiffer has achieved seamless end-to-end connectivity, shorter lead times and increased throughput.
Read MoreThe CNC Reveals its Secrets
Machine monitoring becomes a platform for predictive maintenance without requiring extra sensors.
Read MoreRead Next
Using Automation to Reduce COGS and Stay Globally Competitive
Decade-long, multiphase automation investments lower operating costs and maintain technology lead in an increasingly competitive global market.
Read MoreObscure CNC Features That Can Help (or Hurt) You
You cannot begin to take advantage of an available feature if you do not know it exists. Conversely, you will not know how to avoid CNC features that may be detrimental to your process.
Read More3 Mistakes That Cause CNC Programs to Fail
Despite enhancements to manufacturing technology, there are still issues today that can cause programs to fail. These failures can cause lost time, scrapped parts, damaged machines and even injured operators.
Read More